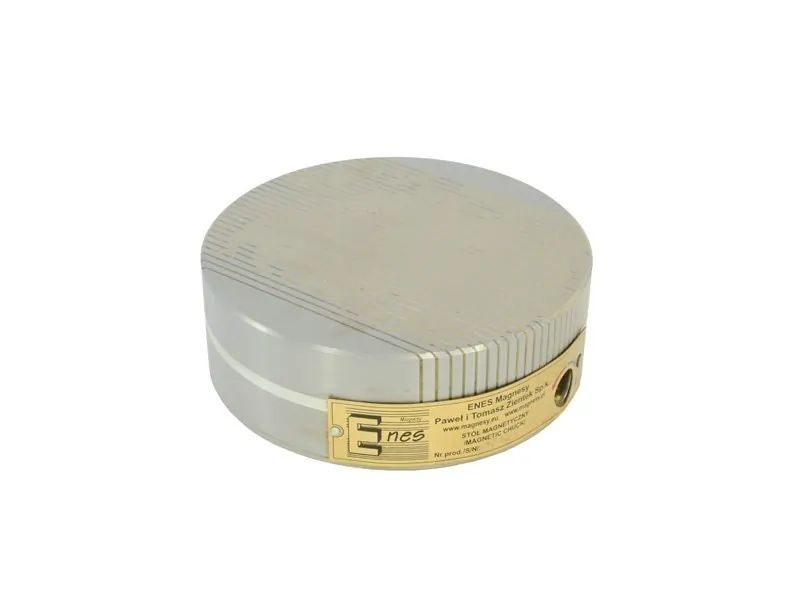
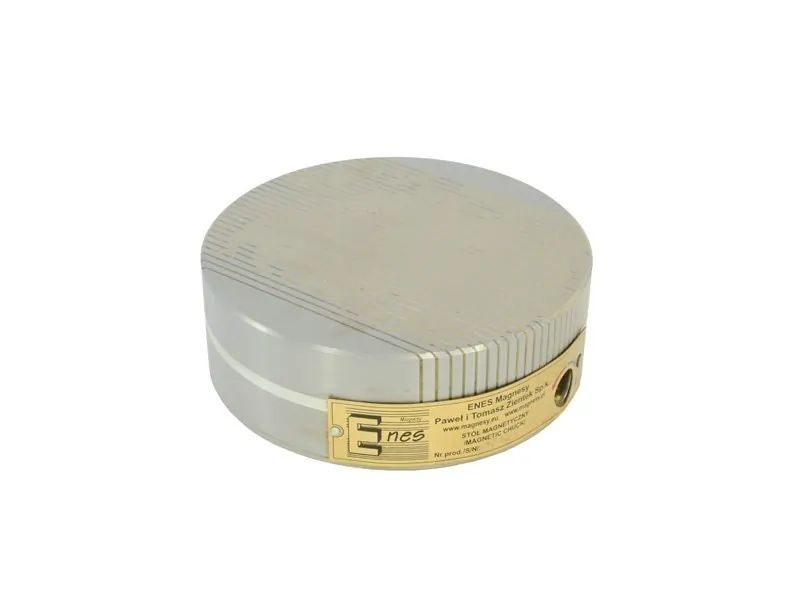
Polityka bezpieczeństwa (edytuj za pomocą modułu „Bezpieczeństwo klienta”)
Zasady dostawy (edytuj za pomocą modułu „Bezpieczeństwo klienta”)
Zasady zwrotu (edytuj za pomocą modułu „Bezpieczeństwo klienta”)
TC series circular permanent magnetic chucks are designed to clamp ferromagnetic workpieces (iron, structural steel, alloy steel, cast iron) during grinding, milling and electrical discharge machining. In the case of materials with high magnetic properties (steels with high iron content), the chucks can be used as holders in turning operations.
The chuck can be mounted using the grooves at its bottom or the four threaded holes (see the attachments). The body of the chuck consists of a single block of steel, while its top plate is made from steel and brass lamellas placed interchangeably. TC series circular chucks use neodymium magnets, so that a maximum magnetic holding force of approx. 100 N/cm2 is achieved. The magnetic field can be turned on with the use of a lever (Allen wrench), by turning the lever to the right by 180o. To turn the field off, the lever should be turned inversely.
The rigid structure of the chuck enables very precise machining, while its tightness allows using the chuck for operations involving coolant or operations in full submersion. The simplicity of the design ensures a long and reliable operation of the device. A lack of electrical power supply makes the chuck completely safe during the operation. The pole pitch (3.0 + 1.0 mm) enables firm clamping at a small height of the magnetic field, so the workpieces clamped can be thin.
Pole pitch diagram:
The clamping force depends on the following parameters:
- Armco iron 100%
- low-carbon steel 90% (St3s)
- high-carbon steel 80% (St45)
- alloy steel 70% (Corrax)
- high-alloy steel 65% (1.2436)
- cast iron 50%
- for Ra up to 0.08 µm 100%
- for Ra up to 0.20 µm 90%
- for Ra up to 1.25 µm 70%
- for Ra up to 6.30 µm 50%
- for Ra up to 25.00 µm 30%
The circulair permanent magnetic sine chucks available in our offer are presented below:
Type of the chuck | Dimensions [mm] | Weight [kg] | ||||||
D | H | L | Pole pitch | D2 | D3 | M | ||
TC-110B | 110 | 50 | 80 | 3+1 | 70 | 90 | 4x M8 | 4,6 |
TC-125B | 120 | 52 | 95 | 90 | 110 | 4x M8 | 5,5 | |
TC-150B | 150 | 50 | 117 | 110 | 130 | 4x M8 | 6,5 | |
TC-160B | 160 | 52 | 129 | 120 | 140 | 4x M10 | 7,5 | |
TC-200B | 200 | 55 | 169 | on request | 11,5 | |||
TC-250B | 200 | 55 | 213 | on request | 19,5 | |||
TC-300B | 300 | 55 | 270 | on request | 27,5 |